Industry News
Environmental factors, such as temperature and vibration will often have a negative impact on the performance of a precision motion system. Engineers go to great lengths to find ways to control temperature and isolate vibrations. Adding either cooling or heat dissipating devices, use of exotic materials, or active vibration dampers ultimately add complexity, cost and can impact reliability.
Nanomotion’s Solution – Leveraging the B2 Mode:
Nanomotion’s core motor technology is based on an L1 / B2 excitation of a piezo crystal, at a resonant frequency, to generate an elliptical motion at the ceramic tip. In addition to this ultrasonic standing wave, THE SAME MOTOR can be used in a B2 mode only, generating the ability for thermal compensation or vibration suppression from the sub-nanometer level to several hundred nanometers.
The “DC Mode” within Nanomotion’s product line allows the seamless switching between an ultrasonic mode and a bending mode. The bending mode leverages standard piezo actuator principles, with sub-nanometer resolution and the ability to operate over +/-300nm, up to 1kHz.
The “Y Axis” graph shows the controller output, as the temperature is changing to maintain a position within +/- 2nm. The controller output line is a mirror image of the actual temperature, demonstrating the ability to maintain system precision under varying temperature.
The “Temperature” graph, reflecting a 500mm travel, shows the environmental temperature fluctuation. The purple line represents the temperature of the air, with the other lines representing the temperature on the motion axis.
The Axis below is subjected to an external vibration, creating a 78nm disturbance (position error), seen on the encoder. This is reflected it the large sinusoidal curve on the left side of the graph. This disturbance is measured and compensated for, when we turn on the DC mode. The vibration suppression brings the axis to a stable position within 6nm, a factor of 13 improvement, eliminating the impact of the vibration.
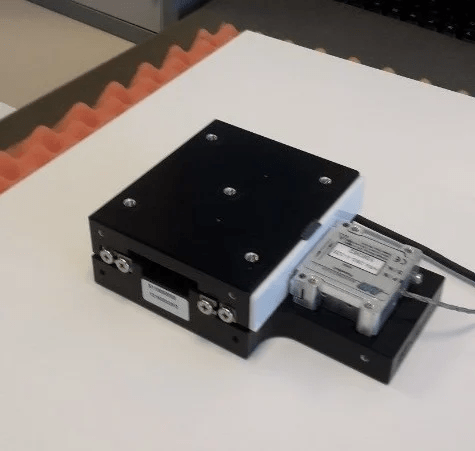
The multi-function capability, managed at the drive motor level, designed into a single axis can eliminate the need for cumbersome external temperature and vibration compensation. As motion systems strive to meet the performance demands of the next generation of semiconductor tools or face the challenges of vibration from airborne optronic systems, the ability to utilize the dual modes designed into the same axis, provides unmatched performance, improving precision and system reliability.
For a complete understanding of system designs and performance levels, please contact Nanomotion at nano@nanomotion.com or +1 (631)585-3000, or visit www.nanomotion.com.
About
Utilizing proprietary technology, Nanomotion designs and manufactures complete motion solutions from start to finish.
Motion Solutions By Industry